Technical Paper
Improvements in offshore pipeline cathodic protection and anode life extension
by Jim Britton (2006)
Abstract
New deep-water discoveries combined with current high energy prices have given much of the world's aging offshore infrastructure a new lease on life. Offshore pipelines in particular are at the highest risk of catastrophic external corrosion failure if their cathodic protection systems are allowed to fall into disrepair. Newly developed survey methods, combined with innovative design software and low cost hardware, are helping take the pain out of asset life extension for many operators worldwide. This paper briefly presents some case histories and discusses the methods used and the overall strategy driving them. The deep-water revolution is also presenting new challenges in offshore pipelining. Methods combining cathodic protection and simplified life-cycle monitoring exist; they will be touched on in this paper.
Introduction
Cathodic protection methods for offshore pipelines have not changed very much in the last 40 years. This is surprising, because every other aspect of offshore pipelining has undergone radical improvement over the same time period. Coatings have evolved from old mastic-based systems to ultra-reliable three-layer systems (thermally insulating coatings etc). The old lay barges have been replaced with sophisticated purpose-built pipe lay vessels. As a result, pipes can be reeled and laid with maximum efficiency. Perhaps cathodic protection engineers were the only ones to get it right from day one? Obviously not - the bracelet anode has a lot of shortcomings; the only reason it hasn't changed is because it has been accepted into offshore lore. We are about to see that a change is just around the corner. After 40 years plus, we are finally due! The writer's company has been at the very forefront of this industry for the past two decades. This paper will show the future of pipeline cathodic protection and will dispel many frequent misunderstandings about external corrosion control for offshore pipelines.
Pipeline survey inspection and monitoring
This area is one of the writer's "pet peeves" regarding our industry. The early days of doing cathodic protection surveys on offshore pipelines (1970's predominantly) borrowed directly from onshore methods and came up with the dreaded tow fish trailing wire survey. The flaws of this type of survey are widely understood. However, habits seem quite hard to break. Millions of dollars have been wasted by operators trying to get meaningful information using this method. To now admit that it was all a waste of time and effort is difficult for many who have either misled or have been misled. But the fact, like it or not, is that the data from tow-fish surveys are worthless and often times dangerously optimistic. But take heart; most pipelines were not at serious risk for the first 25-30 years of their life anyway. The first time a technically correct method is used, a sound baseline for future integrity management is established, and those old data no longer have any value at all.<
How should it be done?
The ROV-assisted three-electrode technique was pioneered in the North Sea in the late 70's and early 80's. It was the first time true close-interval offshore potential data were available. It is now the most widely-used survey method for areas where an ROV can be used effectively, and when correctly calibrated, produces the most accurate data available. Whether or not it is necessary to gather this much data or spend this much money to verify the condition of a pipeline's cathodic protection system is arguable.
What options are there?
The options that are available are driven by the amount of information required. If a potential reading is required at 1-meter intervals along a pipeline, then you are stuck with the ROV and three-electrode approach. How about a data point every 200 meters, or a data point every 10 km? Could this be enough information? The answer is "yes," provided that it's the right type of information. Short order changes in protection levels of coated offshore pipelines are very predictable and do not occur in the same way that they can onshore. This can be verified by analysis of the tens of thousands of miles of three-electrode data that has been processed over the last quarter century. In truth, we can make an accurate assessment of a pipeline cathodic protection system with relatively few accurate and repeatable data points. This ability is further enhanced if there is an accurate baseline survey available.
• The CP Snake (no longer available) was a BLF survey method (bottom-towed, lateral, field gradient) using the same basic 3-Electrode methodology but making lateral intersects with the pipeline and running on the seabed. With this method, an accurate data point is obtained at whatever interval the operator requires but generally 200-300 meters spacing. This is enough data to positively verify the pipeline cathodic protection status. The nature of the BLF survey ensures an accurate and verifiable data point, unlike the old trailing-wire tow-fish method, and offers the same general low cost.
• Depending on local diver / ROV costs, another option is to take periodic subsea contact potentials at reasonable distance intervals, or to install permanent monitors at key locations and read their data with divers or low-cost ROVs. The extent to which these methods can be usefully employed depends upon the particular pipeline and the local regulations. The important point is that it is not necessary to have thousands of data points to accurately access cathodic protection status on an offshore pipeline.
• Recently updated pipeline design codes (ISO, DnV, NACE) stress the importance of attenuation modeling as a design aid. Attenuation models predict the potential distribution along a pipeline at various distances from known cathodic protection (CP) current sources attached to the pipeline. And knowing potential distribution can be useful not just during pipeline design, but also during the life-cycle maintenance of the pipeline. Thus, it is fully acceptable to predict the worst-case potential at the mid-point between two known current source drain points. This fact can be put to good use when a pipeline is retrofitted with intermittent anode sleds. Once we have measured the potential at the drain point (point of connection of the anode sled to the pipeline) and the mid-point pipeline potential between sleds and the current output (EFG) associated with each sled, we have a good baseline from which to develop a life-cycle maintenance/survey program. Interval surveys need only consist of drain point measurements; potential attenuation modeling can do the rest.
Attenuation modeling
There are a number of critical variables, which will affect the accuracy of any model. These variables occur on both sides of the reaction:
Key cathodic variables
1. Coating condition, size, number and linear distribution of coating defects(Most models either assume worst case or linear distribution of damage at a given coating breakdown percentage).
2. Pipeline material and wall thickness.
3. Pipeline operating temperature.
4. Exposed or buried (Most models assume worst case (pipeline exposed, anodes buried).
Key anodic variables
1. Anode array to environment resistance, including connection resistance.
A successful model derives input from a logical analysis of the situation; this means putting into the model what we believe to be the true condition of the pipeline and its anode system. For new pipelines this is relatively easy. For old pipelines it can be easy if we have accurate and meaningful survey data. The application of attenuation models in offshore pipeline retrofit design is critical to keep the costs of this type of work under control. When one considers that the cost of a pipeline retrofit offshore is virtually directly proportional to the number of dives that have to be made, it is clear that optimization of anode sled spacing offers a significant benefit.
Retrofitting an existing offshore pipeline
Forward thinking operators in many areas of the world are realizing the value of offshore pipelines. Not only as a high integrity transport to support ongoing oil and gas operations, but as an in-place conduit that could be used for other energy related purposes in the future. Given that the cost to maintain the pipeline in good condition for decades at a time is relatively low, there are many offshore pipeline cathodic protection retrofit initiatives worldwide.
There are three main reasons to retrofit and maintain offshore pipelines against external corrosion.
1. The original system has depleted, and the integrity of the pipeline has to be maintained.
2. The pipeline will be required to serve beyond its original design life (original anode designs are 25-30 years).
3. Damage to the coating or anode systems either during or post installation.
The methodology to follow is basic:
1. Assess the condition of the pipeline. There are optional strategies to follow. [1]
2. Calculate cathodic protection requirements / develop anode array physical design and optimized spacing on the pipeline.
3. Define connection method for connecting anodes to pipeline.
4. Install the system.
5. Conduct a baseline post-retrofit survey (this is the NEW baseline, all previous survey data are of NO VALUE at this point.)
Deepwater has completed many successful pipeline retrofits based on all of these conditions. The projects have been completed efficiently with ROV's and/or divers. The key elements to our success are:
1. Proven attenuation model packages.
2. Using only accurate survey methods.
3. Anode sled designs optimized for any condition of current, life, installation method and ocean bottom condition. [see Figures. 1-3]
4. Reliable ROV or diver anode sled connection systems. Systems that eliminate the need to fully expose the pipeline or to remove any concrete weight coating. [see Figure. 4]
5. Simplified life cycle maintenance options
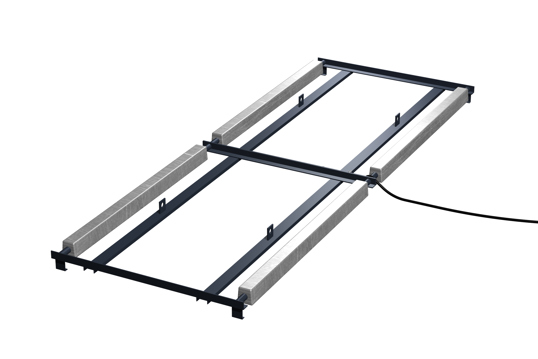
Figure 1 - RetroSled™
Rigid sacrificial aluminum anode sleds for offshore pipeline cathodic protection retrofit. Best on firm, sandy bottom conditions. It has a low scour tendency and 3-4 Amps of cathodic protection output.
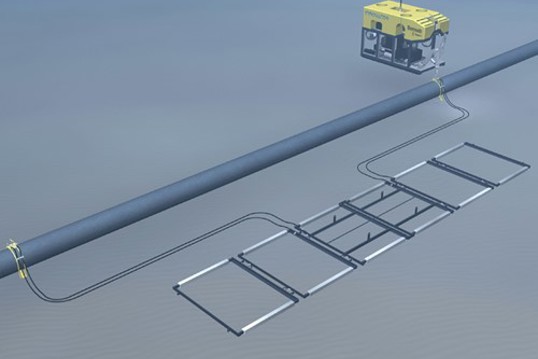
Figure 2 - Expanding RetroSled™
ROV installed sled that is opened up on bottom. Best on soft bottom conditions. It has a mild scour tendency and 4-6 Amps of cathodic protection output.
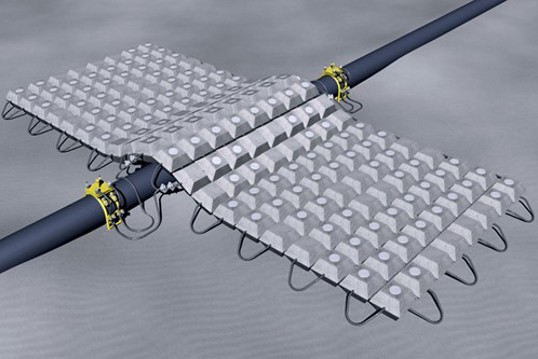
Figure 3 - RetroMat™
Combined concrete stabilization mat and aluminum anode system. Can be used in any conditions. The mat produces 1-5 Amps of cathodic protection output.
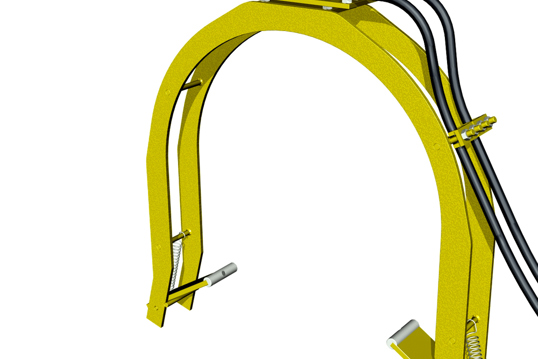
Figure 4 - RetroClamp™
Provides monitored connector between the anode arrays and the cathode.
A sample case history summary
12" Oil pipeline 35 miles long (Gulf of Mexico) Retrofitted 2000
Saturation dive spread operating from 4-Point DSV. 225 feet sea-water max.
60% of pipeline buried >3 feet.
14 Dual Sled installations installed at approximately even spacing on pipeline.
Installation time: 7 days
Project cost: $415,000.00
New pipelines in deep water
Pipelines in deep water should not be treated like pipelines in shallow water. There are key differences that translate into obvious key strategy changes when dealing with the subject of corrosion control.
1. The key to maintaining long-term corrosion protection on a deep water pipeline is the quality and integrity of the coating system. Thus, installing bracelet anodes is completely counter-productive in that the pipe's coating is unnecessarily compromised at every anode installation point (e.g. hundreds of sites on a 20 mile pipeline). Moreover, anode attachment often requires an interruption in the lay procedure, which translates to higher installation cost and reduced efficiency.
2. If we get a 99 percent efficient coating on bottom we can use a variety of smart (self monitoring) cathodic protection systems to protect miles of pipeline from a single, easily-monitored installation. This capability is further enhanced in deep water, since anode structures can be engineered to operate in the water phase (Figure 5), rather than getting buried in the mud (which decreases anode efficiency).
3. Deep water pipelines often have special coatings for thermal insulation. These coatings are often violated during anode attachment - a most undesirable event. Pre-installed anode connection rings can be engineered into field joints to allow ROVs to post-install smart anode arrays and tie-backs every 5 miles (or whatever the optimum distance may be).
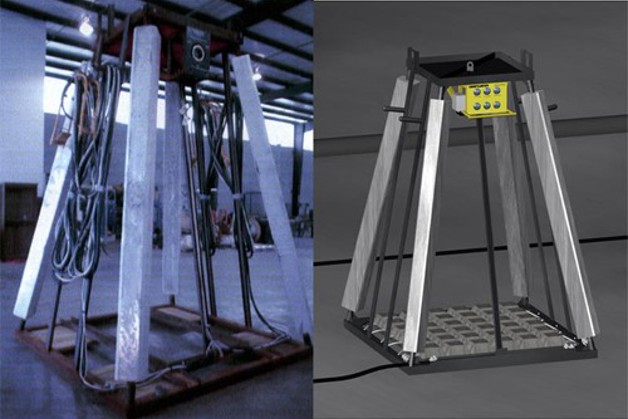
Figure 5A - Smart anode pod structure
(Early smartpod model) Cathodic protection system for deep water pipelines. Includes pipe clamps (Retroclamp) and integral Sunstation™ cathodic protection monitor, which outputs the cathodic protection potential measurement taken on the many reference electrodes attached to the system.

Figure 5B - RetroPod XL structure
(from 2013) Cathodic protection system for deep water production equipment. Includes Retroclamps and integral Sunstation readouts, to protect and monitor up to six pieces of subsea production equipment.
In realization of these points, recent updates to the relevant codes of ISO and DNV recognize these methods as appropriate, and they have design guidelines for remote anode cathodic protection systems and new pipeline coating efficiency rules to correspond.
Summary
Ensure that all elements of your asset integrity management program rely on unquestionable survey information. Utilize the newest technology available to provide efficient and verifiable cathodic protection performance. For new construction focus on high-performance coatings with widely spaced smart cathodic protection stations (like onshore systems).
References
1. J. Britton "Offshore Pipeline Retrofit Strategies" CORROSION 2006
Want to receive an email when Deepwater publishes new corrosion-related technical papers, case studies, and more? Sign up for our Corrosion Newsletter using the form below. You can unsubscribe at any time.