Dudgeon CP Monitoring
Remote cathodic protection monitoring system installed in the North Sea
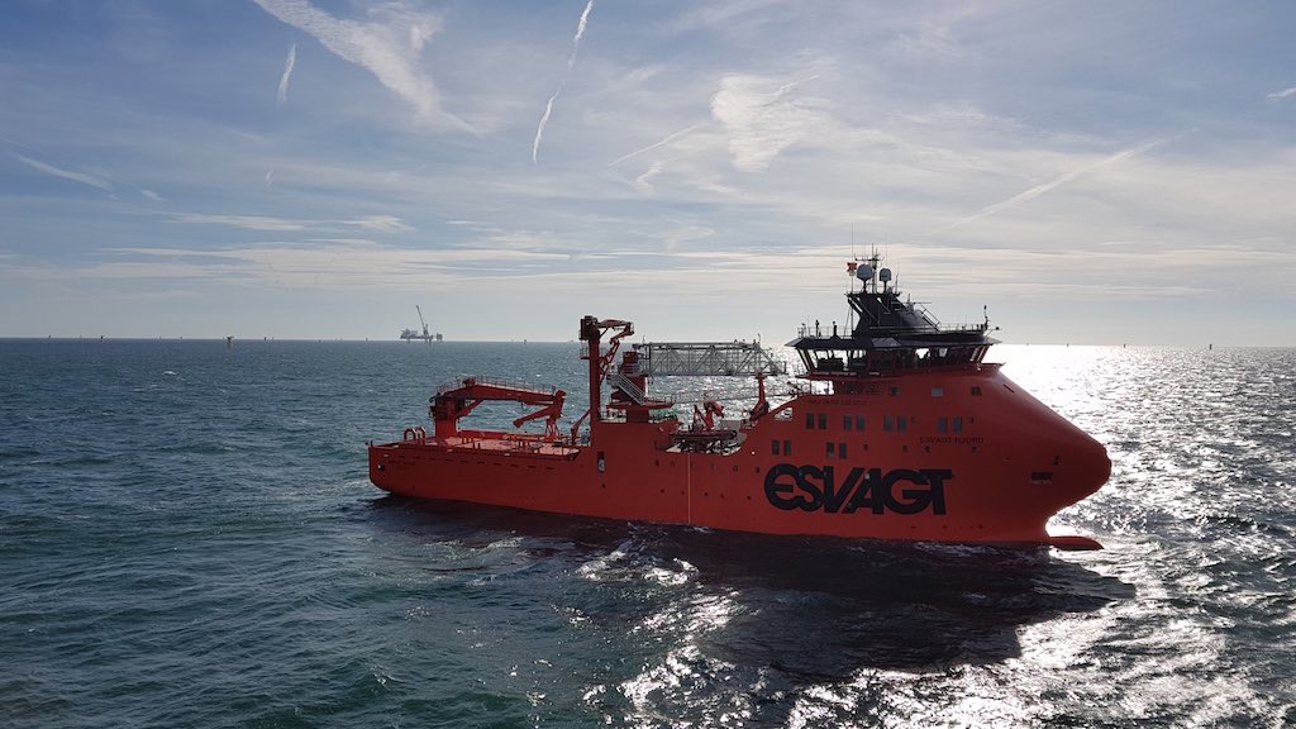
Introduction
Due to the global drive to move away from the use of fossil fuels for energy production, successive British governments have worked to increase the proportion of renewable sources into the energy mix. Renewable sources of energy have gone from 2.5% in 1990 to almost 20% in 2014, with the large proportion of this coming from both onshore and offshore wind farms (9.4%). The UK is considered one of the best locations for wind energy production in Europe and rapid increases in capacity are in progress with more planned. Installing and operating offshore wind farms is presenting the industry with numerous challenges to ensure that the wind turbine generators remain protected externally from corrosion throughout their design lives. Traditionally, steel structures are protected from corrosion subsea by sacrificial anodes arranged evenly around the surface area. However, the monopile design of wind turbines means that a bank of anodes mounted near the surface must provide protection all the way down to the seabed. Fast-flowing water in the areas where the wind farms are built reduced the effectiveness of the cathodic protection (CP). As future construction is foreseen into deeper waters, these problems could be compounded. Due to the dynamic environment, it is difficult to ensure that the external CP systems on these unmanned structures are operating effectively- however it also makes it more important to do so. The high water flow makes installing fixed sensors for any length of time very difficult, and the cost of repeated site visits by technicians to retrieve the data makes remote access the more suitable option. Deepwater’s rugged monitoring system based upon V-string reference electrodes tethered to a semi-tensioned tether system were selected as a suitable solution to the requirements. Remotely accessed data logging systems powered by PV solar systems were paired with this to minimise ongoing operational costs. Deployment of each of the 4 systems in their entirety took approximately 12 hours.
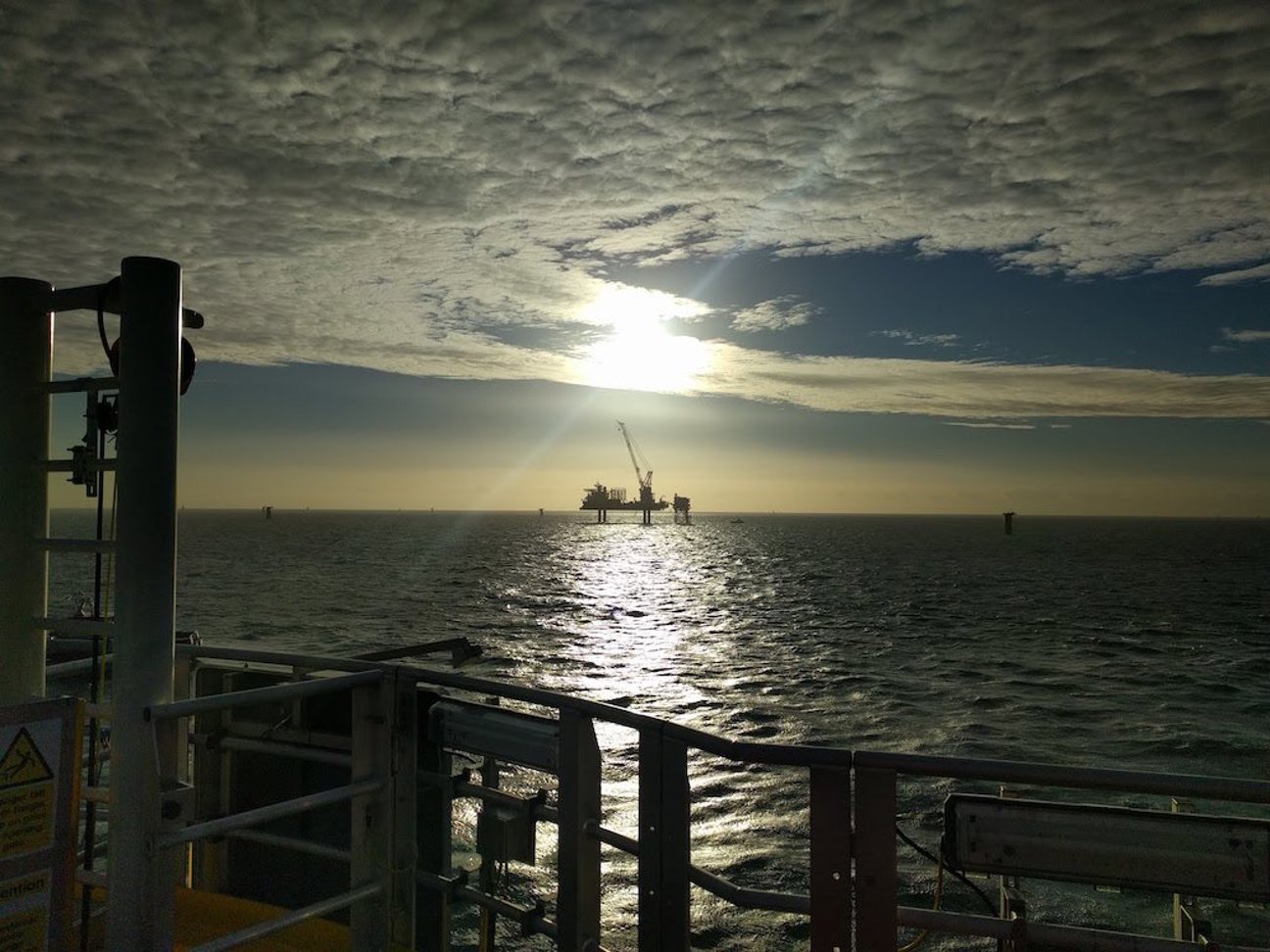
Statoil Dudgeon OWF monitoring
This study has been prepared to provide an overview of project STA7083, the design, fabrication and installation of four external CP monitoring systems for the Dudgeon offshore wind farm (OWF). This document highlights the scope of supply, delivery and installation of the systems, as well as detailing any lessons learned.
Background
The Dudgeon offshore wind farm (OWF) is a new development currently in construction to be operated by Statoil ASA. Dudgeon OWF is located 32 km off the north Norfolk coast, with a stated capacity of 402 MW generated via 66 No. Siemens 6 MW wind turbine generators (WTGs). All foundations have been driven, with projected installation of the WTGs and final rock dumping during 2017.
To provide assurance that the installed external galvanic CP systems on the structures are providing the required protection, Statoil identified a need for fixed CP monitoring systems to provide confirmation of adequate CP performance. Measuring and recording reliable, repeatable CP readings from fixed locations and depths in the high-flow tidal areas of the OWF is difficult, yet vital for ensuring that the anode systems are meeting their design criteria. It was planned for the monitoring systems to be installed during the early stages of the field construction, so that the early CP polarisation data could be gathered and any long term seasonal variations identified and further monitored.
Deepwater provided a short optioneering study to Statoil, leveraging different approaches to mounting and routing the subsea sensors to minimise risk of system failure. Communications and data integration options were also explored. The final design was chosen as the most mature of the options, being a development of previous remote monitoring systems developed by Deepwater and provided to various operators.
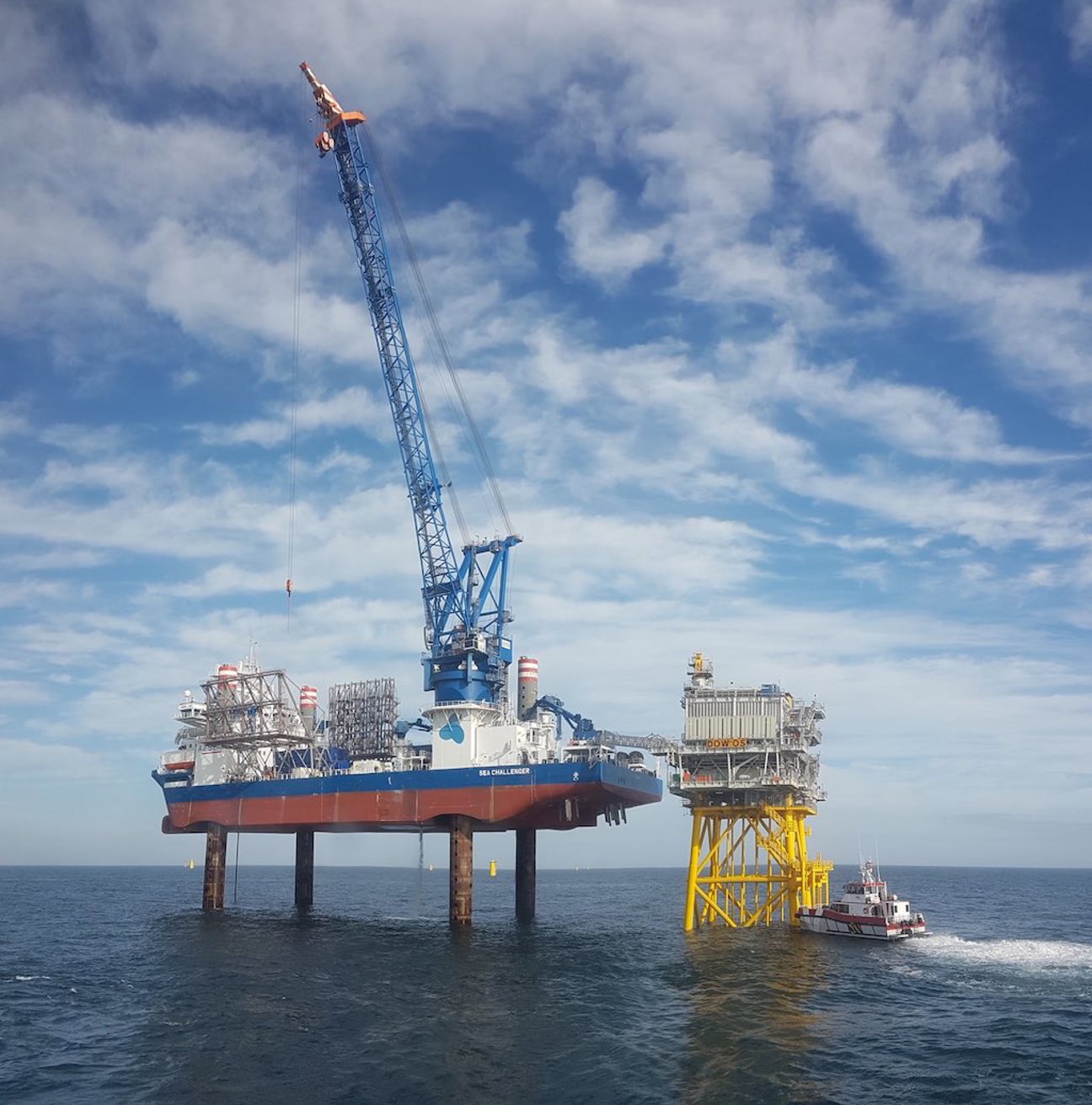
Scope of supply
Detailed design was carried out by Deepwater utilising lessons learned from previous installations for offshore wind and the specific requirements of the Dudgeon OWF. The requirement for data from the initial stages of the construction of the field called for a self-powered system which was not reliant on communication via the field SCADA network. Alterations or additions to the structure of the WTG were not possible, so all the components of the system had to be designed in such a way that they would be securely fitted to the already-installed transition piece without impeding access or operation in any way. Finally, the monitoring system was to be installed on the TP’s external work platform using topside rope access teams and with the assistance of the service operation vessel (SOV) which provides support to work scopes being carried out in the OWF- no jack-ups or subsea intervention was available.
The final system design consisted of a topside unit with data logging and remote communication capabilities for the storage and transmission of data from the 3 zinc V-string reference electrodes to be installed per structure. The monitoring and communications equipment comprised of off-the-shelf (OTS) components, configured specifically to meet the project’s requirements. This provided a cost saving over a fully custom system, while still providing the full functionality required. The monitoring and communication system was powered by a solar array with a back-up battery bank. This provides reliable standalone electrical power even during winter months due to the carefully managed power configuration optimised by Deepwater’s engineers.
The subsea component comprised a weight mattress connected to the WTG above the waterline via a synthetic tether with the CP potential electrodes attached at specific points along its length. The FLXMAT system was selected as the most suitable solution to provide the ballast; Rather than using a reusable steel mould, the concrete is cast directly into plastic shells that stay in place meaning there are no sharp edges that could damage the cable. Incidental impact damage to the TP coating during installation is also minimised, as is the potential for injuries due to concrete dust and particles. The tether was selected for its high breaking strain, as well as its seawater, corrosion, UV and abrasion resistance. The weight mattress and tether components were specified to withstand the high current and weather conditions expected in UK coastal regions, based upon modelling carried out by third-party design engineers. The tether was part-tensioned via an attachment to the middle rest platform of the TP, keeping the whole assembly clear for safe access of the WTG while ensuring that the reference electrodes remained at fixed points in the water column.
The V-string zinc reference electrode provides long-term, stable CP potential measurements and was selected for this application due to its rugged construction. The zinc reference electrode is far less fragile than a silver / silver chloride equivalent, with a longer reliable design life, both of which are advantages in dynamic environments where replacement is not envisaged. The cable tail is especially toughened and sheathed with an abrasion-resistant synthetic braid, further improving protection. A total of 3 reference electrodes per structure was chosen, with one positioned below the level of the rock dump, another just above the rock dump layer and a third one at the mid-point of the submerged section.
The scope was to provide four systems to be installed on representative WTGs throughout the field. The materials supply was completed by Deepwater EU in the UK, with the separate components consolidated and delivered to Great Yarmouth, UK in time for loading and deployment according to the project schedule.
Installation
Installation of both the topside units and the subsea components was carried out under Deepwater supervision, both on the vessel and the structure, with support from rope access technicians from Trac and the crew of the client’s Service Operation Vessel (SOV), the Njord, operated by Esvagt under the control of Statoil client representatives.
The entire system was installed without any subsea intervention by diver or ROV; cameras attached to the crane hook and acoustic release systems were leveraged to remove the requirements and keep installation costs down. Rope access teams supported the topside routing and fitting of the tether tensioning system and monitoring systems.
Weather conditions were a limiting factor due to the minimal distances between the vessel, the crane, and the WTG structure. However, all elements of the installation and commissioning work scope were completed successfully and ahead of schedule.
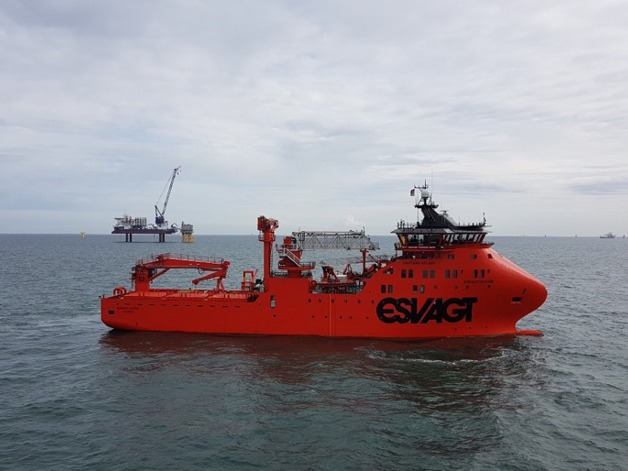
Results
The following are the results and lessons which can be taken from the project and applied to future, similar jobs.
- Fixed CP potential reference points have been installed on four representative structures at an early stage of construction - giving an indication of polarisation behaviour and ensuring/validating the CP design for the OWF.
- The system was very simple to install, with the systems being rapidly deployed by the installation team using the SOV- approximately 1.2 days per system (exclusive of downtime due to weather days etc.).
- Integration of personnel from four separate companies was highly productive and valuable knowledge and experience was transferred between all parties in order to improve the delivery of the project product.
- CP data can be remotely accessed without needing technicians to directly access the site, decreasing O&M costs and workload.