Technical Library
Filter your selection
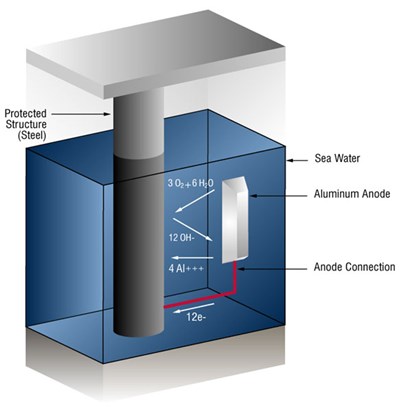
Cathodic Protection 101
This paper is a basic introduction to the scientific concepts behind cathodic protection. Intended for internal training. The topics covered are: anodes, cathodes, sacrificial or galvanic cathodic protection, impressed current cathodic protection (ICCP), the basic chemical formulas describing cathodic protection, testing and monitoring a CP system.
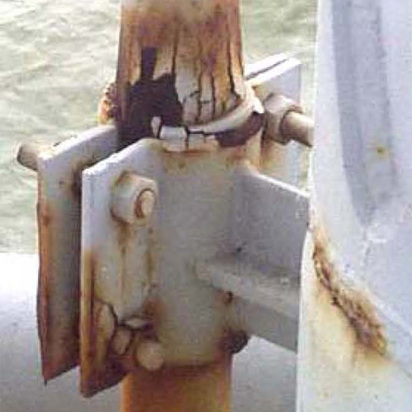
Corrosion at pipe supports
Corrosion at pipe supports is one of the leading causes of topside process piping failure.
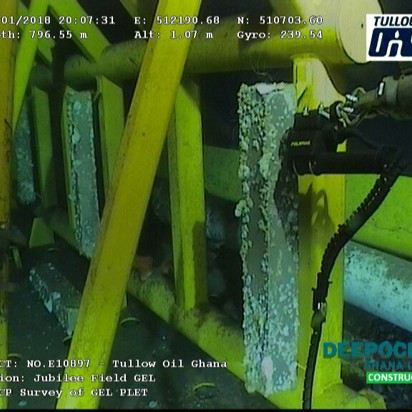
CP survey confirms integrity of Jubilee field subsea equipment
To help Tullow Ghana Ltd. (Tullow Oil) meet its commitment to safe and reliable operations, Deepwater Corrosion Services, Inc. was selected to prepare and execute a cathodic protection (CP) assessment for the deepwater Jubilee field, offshore Ghana.
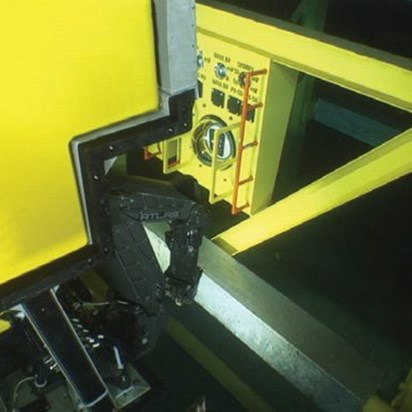
SunStation™ - New solar-powered CP tool helps reduce corrosion risks
The increasing demands on subsea infrastructure to work at greater depths, in harsher conditions, and for longer design lives requires a new look at the tools and techniques used for cathodic protection (CP) monitoring. This is increasingly important in today’s world, where regulatory oversight and the need to effectively manage risks is paramount.
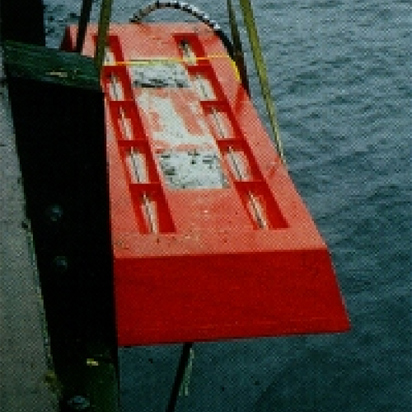
Impressed Current CP retrofits on offshore platforms
It has long been recognized that an impressed current cathodic protection systems can offer significant economic advantages over galvanic anodes.
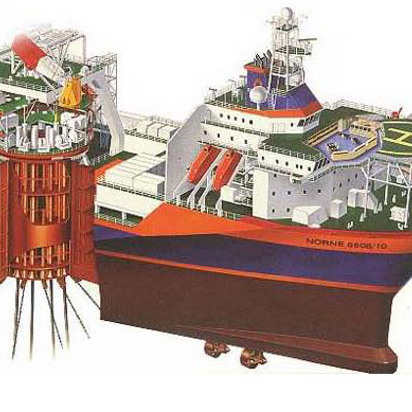
Cathodic protection system strategies for FPSOs
FPSO (Floating Production Storage and Offloading) structures present some interesting cathodic protection challenges. Are they ships or floating production platforms? Is impressed current cathodic protection the way to go? How do we handle protecting the ballast tanks? What about the mooring systems?
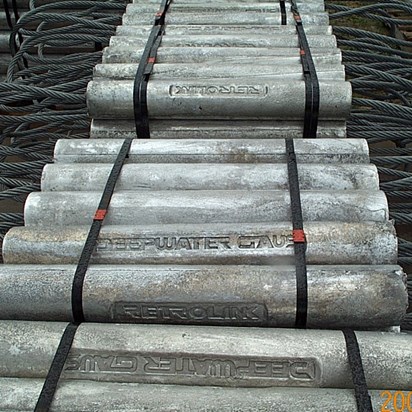
IMR Heaven - IMR ready retrofittable cathodic protection system for offshore brownfield fleets
The RetroLink™ is one of the most versatile anode systems on the market. Deepwater has gathered the expertise to apply this anode system to a wide variety of CP projects, and it brings brownfield life extension costs under control, while providing predictable and reliable service.
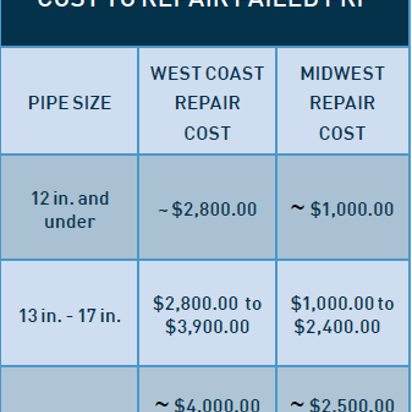
The cost of a bad pipe support
Pipe support failures can be traced back to a poor decision in the initial design, purchasing, or installation of the supports. No two failures are exactly the same, but they all have one thing in common: they cost the operator money in repairing a failed support.
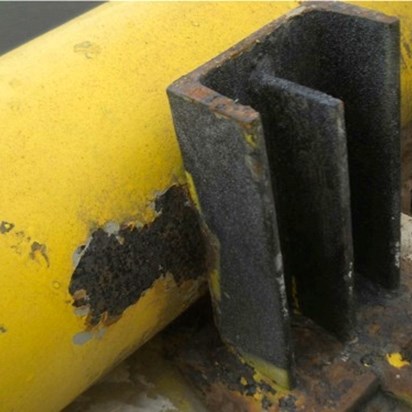
Why these 5 common pipe support designs fail
Various common pipe support designs forget a very simple fact: Crevice corrosion can quickly cause dangerous leaks.
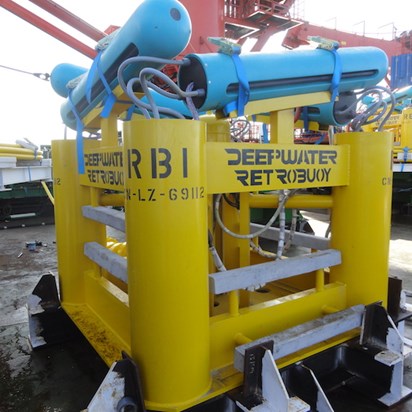
Continued operation of large offshore platforms requires innovative new CP systems to be retrofitted
Many large structures, and other offshore producing areas in the North Sea, are needing to stay operational beyond their original design life.
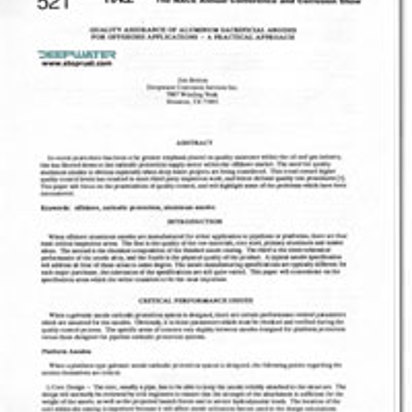
Quality assurance of aluminum sacrificial anodes
In recent years there has been a far greater emphasis placed on quality assurance / quality control within the oil and gas industry. This has filtered down to the cathodic protection supply sector within the offshore market. The need for quality aluminum anodes is obvious, especially when deep water projects are being considered. This trend toward higher quality control levels has resulted in more third-party inspection work and better defined quality-test procedures.
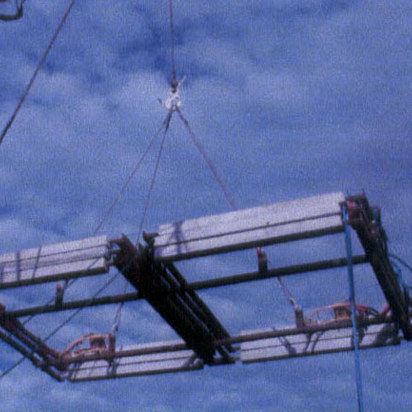
Improvements in offshore pipeline cathodic protection and anode life extension
New deep-water discoveries combined with current high energy prices have given much of the world's aging offshore infrastructure a new lease on life. Offshore pipelines in particular are at the highest risk of catastrophic external corrosion failure if their cathodic protection systems are allowed to fall into disrepair.
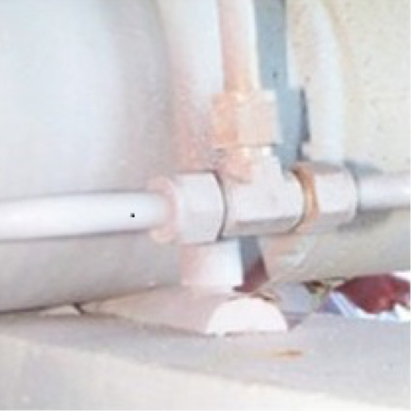
Paper: These are not the I-Rods® you are looking for!
I-Rod's success has spawned many imitation products. While we are flattered, operators should be aware that they can cause costly failures.

Corrosion control methods for deep-water floating production equipment
The rapid growth in the deep-water production sector worldwide has spawned a whole new generation of floating production equipment. This paper will deal with some of the unique corrosion challenges presented by these production systems, and how corrosion is being managed using innovative coatings, new cathodic protection designs and corrosion resistant materials.
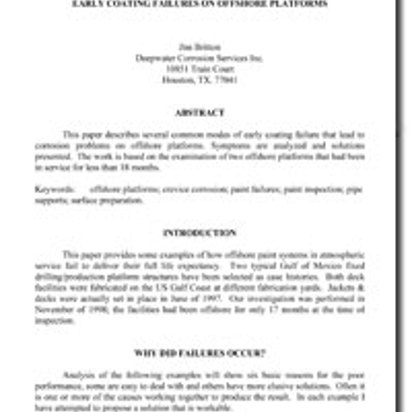
Early coating failures on offshore platforms
This paper describes several common modes of early coating failure that lead to corrosion problems on offshore platforms. Symptoms are analyzed, and solutions are presented. The work is based on the examination of two offshore platforms in the Gulf of Mexico that had been in service for less than 18 months.
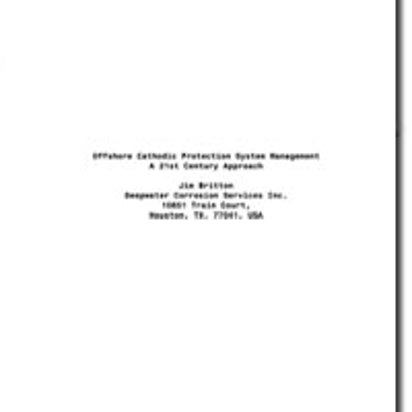
Offshore cathodic protection system management: A 21st century approach
As offshore structures around the world are aging, operators are looking for ways to replace anodes and reduce the costs of doing so (installation).
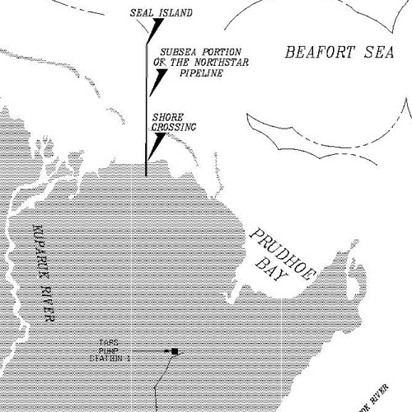
Cathodic protection monitoring of offshore pipelines and structures in Alaskan waters
Pipelines and structures located offshore of Alaska face unique challenges to monitoring cathodic protection. Advances in cathodic protection monitoring technology are discussed. New portable ROV instrumentation as well as fixed monitoring of parameters affecting cathodic protection system performance are reviewed.
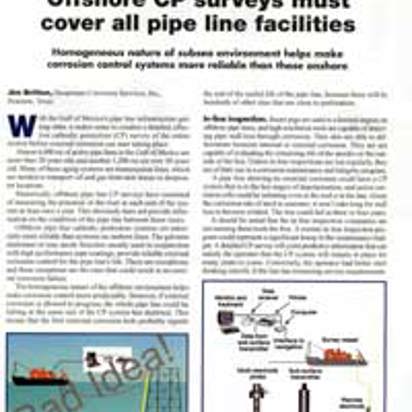
Offshore cathodic protection surveys must cover all pipeline facilities
The homogeneous nature of the subsea environment helps make corrosion control systems more reliable than those onshore. With the Gulf of Mexico's pipeline infrastructure getting older, it makes sense to conduct a detailed, effective cathodic-protection (CP) survey of the entire system before external corrosion can start taking place.
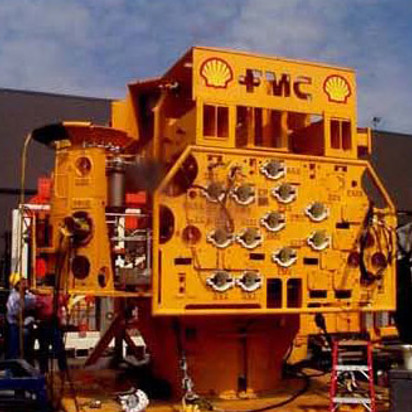
Recent advances in offshore cathodic protection monitoring
Offshore production facilities and pipelines are being installed in new, more hostile environments. Advances in cathodic protection monitoring for new structure types in deep water as well as for high temperatures are discussed. New portable ROV instrumentation as well as permanent monitoring of parameters affecting cathodic protection system performance are reviewed.
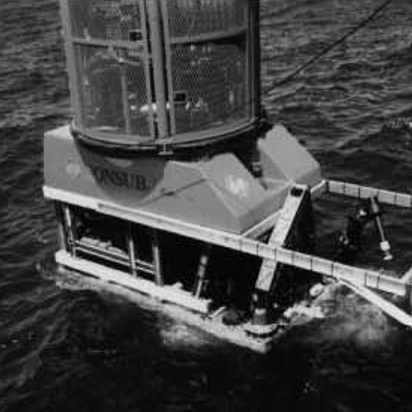
Corrosion control and inspection of deep water pipelines
The external corrosion control of offshore pipelines has, for many years, been accomplished with pipe coatings supplemented with galvanic cathodic protection in the form of zinc or aluminum anode bracelets. This basic methodology works equally well in deep water as it does in shallow. There are, however, some very important differences in the way corrosion control systems operate in deep water versus shallow water.
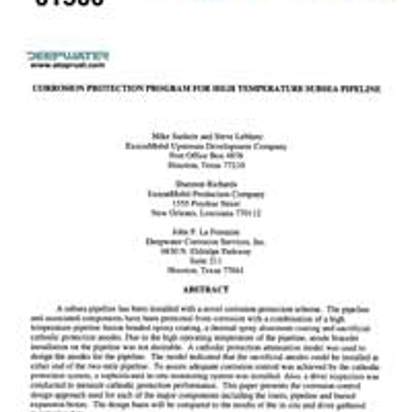
Corrosion protection for a high temperature subsea pipeline
A subsea pipeline has been installed with a novel corrosion protection scheme. The pipeline and associated components have been protected from corrosion with a combination of a high temperature pipeline fusion bonded epoxy coating, a thermal spray aluminum coating and sacrificial cathodic protection anodes. Due to the high operating temperature of the pipeline, anode bracelet installation on the pipeline was not desirable.
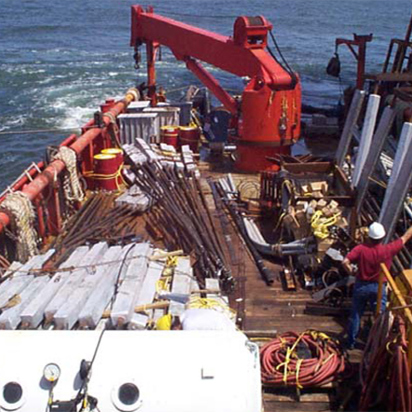
Cathodic protection design in deep water: Be safe, not sorry!
Offshore structures in deep water are now quite common. However, a deep-water development project still requires significant capital investment on the part of the operator. Corrosion failure is not acceptable.

Cost-saving offshore cathodic protection retrofits
Many offshore structures (largely platforms and pipelines) will require a cathodic protection retrofit at some point during their lifetime. This is due to the age limitations of the original cathodic protection anodes and operators' new desire to extend the life of existing offshore infrastructure. This paper explores the conventional methods of anode replacement and compares them to the newer methods developed by Deepwater Corrosion Services and others.
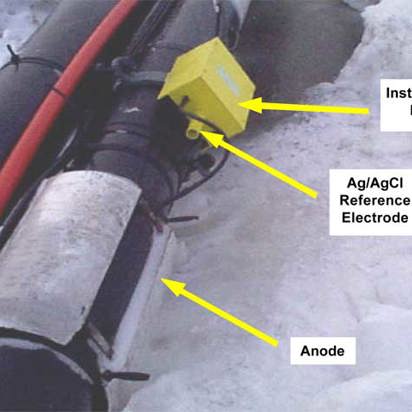
Cathodic protection monitoring of subsea pipelines in the Arctic Ocean
A cathodic protection monitoring system was designed by Deepwater and installed on a recently built pipeline in the Beaufort Sea. The system includes sensors to measure a range of parameters including anode current output, pipeline potential, current density and temperature. This paper discusses the implications of the data collected.
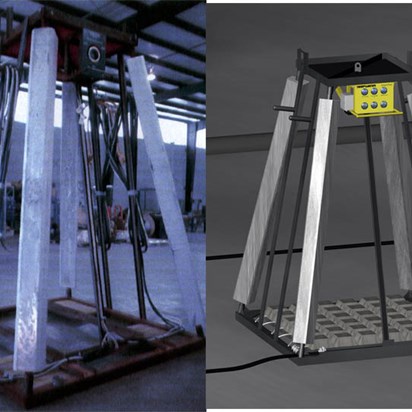
Extending the life of anodes for offshore pipelines: Some new technologies
This paper discusses the practicalities of installing replacement cathodic protection to aging offshore pipelines using diver-assisted and diver-less systems. Current technology for condition assessment and life extension design criteria will be discussed in conjunction with new hardware technologies being utilized to improve reliability and reduce cost of life-extension projects.
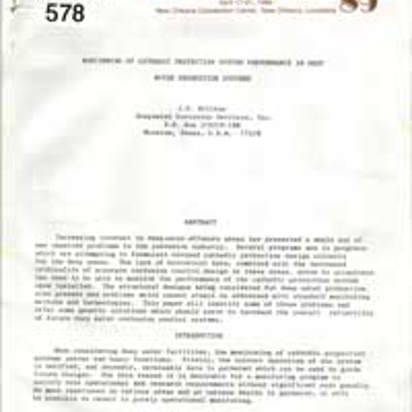
Monitoring CP performance in deep-water production systems
Increasing interest in deep-water offshore areas has presented a whole set of new unsolved problems to the corrosion industry.
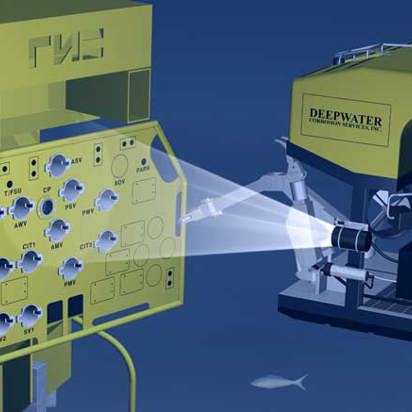
Monitoring CP system performance in deep-water production systems (Part 2)
This paper was originally written for the Corrosion 89 conference, put on by NACE. It was subsequently published in Materials Performance in 1990. In 2005, Mr. Britton wrote an update to address the changes in corrosion control technology for deep water production equipment that had taken place in the interim.
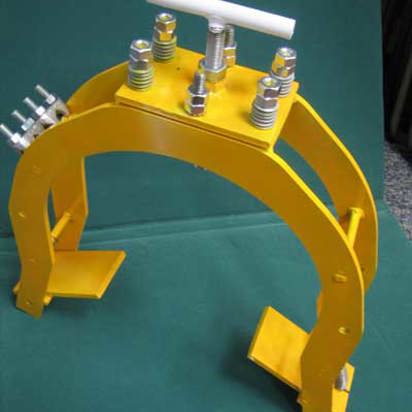
Offshore pipeline cathodic protection retrofit strategies
Many miles of offshore pipelines worldwide are reaching, or have exceeded, the original design life of their cathodic protection systems. Many of these pipelines will be required to function for another 10, 15 or even 20 years. This paper will describe some rational strategies for achieving the desired life extension of the external corrosion control systems at the minimum installed cost.
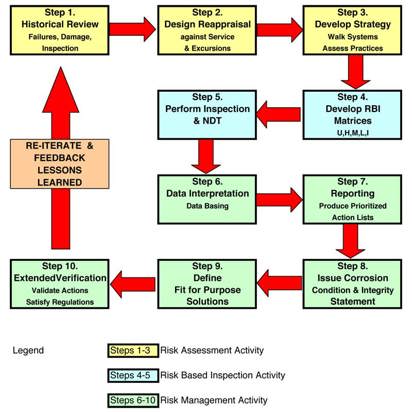
Offshore risk-based asset integrity management: A new methodology
The management of corrosion and integrity for offshore applications has become more critical as deep-water exploration and production continues. There are many challenges ahead, the most important being that the scope for error is greatly reduced. Repair, retrofit or replacement all become that much more difficult and costly due to logistics. The importance of correct execution first time is therefore vital.
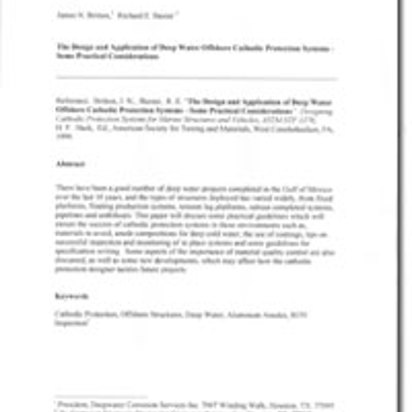
Design and application of deep-water CP systems: Some practical considerations
There have been a good number of deep water projects completed in the Gulf of Mexico over the last 10 years, and the types of structures deployed has varied widely, from fixed platforms, floating production systems, tension leg platforms, subsea completed systems, pipelines and umbilicals. This paper will discuss some practical guidelines which will ensure the success of cathodic protection systems in these environments.
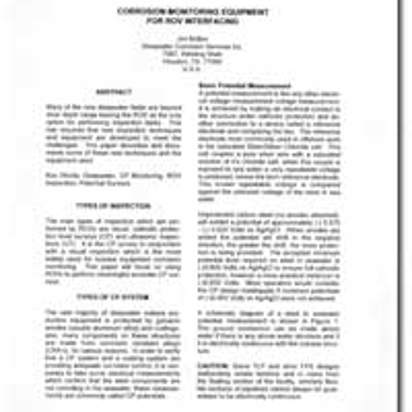
Corrosion monitoring equipment for ROV interfacing
Many of the new deep-water production fields are beyond the depth suitable for divers, leaving the ROV as the only viable option for performing inspection tasks. This fact has caused new inspection techniques and new equipment to be developed to meet the challenges.
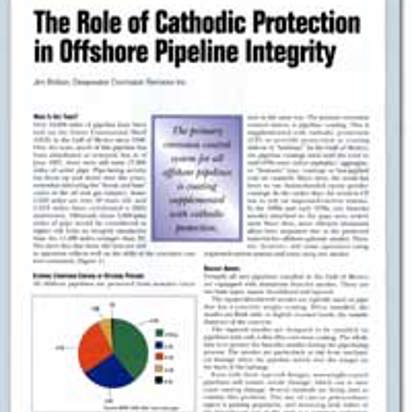
The role of cathodic protection in offshore pipeline integrity
Over 24,000 miles of pipeline have been laid on the Outer Continental Shelf (OCS) in the Gulf of Mexico since 1948. Over the years, much of this pipeline has been abandoned or removed, but as of June 1997, there were still some 17,000 miles of active pipe. Pipe-laying activity has been up and down over the years, somewhat mirroring the "boom and bust" cycles of the oil and gas industry.
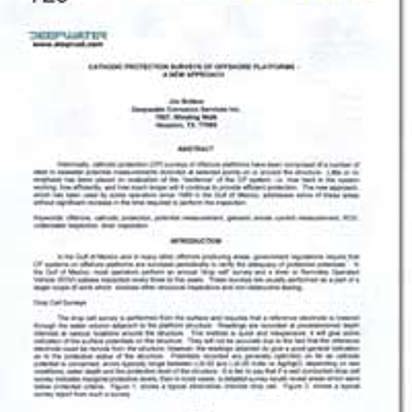
Cathodic protection surveys of offshore platforms: A new approach
Historically, cathodic protection (CP) surveys of offshore platforms have comprised a number of steel to seawater potential measurements recorded at selected points on or around the structure. Little or no emphasis has been placed on evaluation of the "resilience" of the CP system, i.e. how hard is the system working, how efficiently, and how much longer will it continue to provide efficient protection.

Pipe supports: A nagging corrosion problem solved
Why are pipe support points prone to such localized corrosion and what can be done to prevent it? In all cases, localized corrosion begins with coating failure; the presence of water and oxygen then promote corrosion of the exposed steel. The problem is often aggravated by the presence of bimetallic (galvanic) couples and by oxygen concentration differences caused by crevices. The result is a localized corrosion attack which causes significant wall loss.
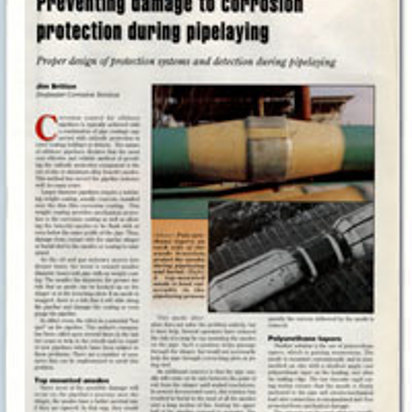
Preventing damage to anodes during pipe laying
Corrosion control for offshore pipelines is typically achieved with a combination of pipe coatings supported with cathodic protection to cover coating holidays or defects. The nature of offshore pipelines dictates that the most cost-effective and reliable method of providing the cathodic protection component is the use of zinc or aluminum alloy bracelet anodes. This method has served the pipeline industry well for many years.
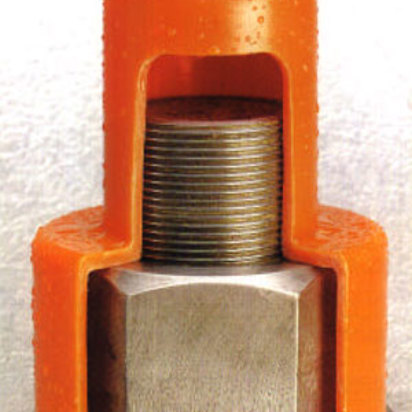
New paint preservation technologies for offshore and marine equipment
Offshore and marine operators - without exception - spend the largest part of their corrosion budgets on paint maintenance. The failure of a “well applied” paint system can be traced to a few basic failure mechanisms. Some of these mechanisms are addressed in this paper. If the solutions presented are applied, then paint systems will last much longer and maintenance budgets can be diverted to other areas.
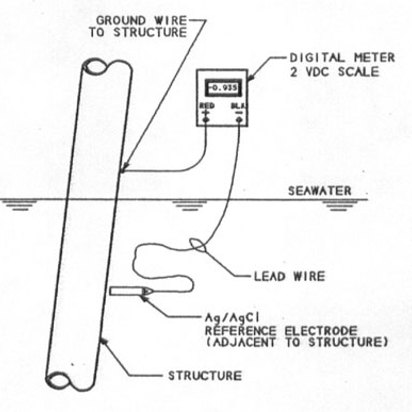
Maximizing the value of underwater CP surveys for offshore platforms
In the Gulf of Mexico and many other operating areas, the measurement of cathodic protection potentials on offshore structures is a regulated activity. Thus, since it has to be done, it makes sense to get as much benefit from the survey as possible. In the majority of cases, this is not being done.
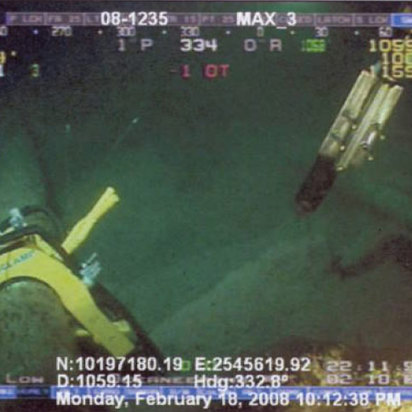
The need for retrofit: Monitoring and CP life extension of offshore pipelines
It is very important to retrofit pipelines that are coming of age, mainly, pipelines that have reached their original CP design life but will continue to be used for a given number of years. The information required in order to perform a CP life extension consists of the following: Pipe diameter, length of pipeline, coating type, the age of the pipeline (construction year), operating temperature, is the line buried or not, water depth and desired life extension (years). Utilizing this information, the CP designer can use industry standards to accurately predict the bare-steel surface area (e.g. ISO-15589.2, DNV-RP-F103).
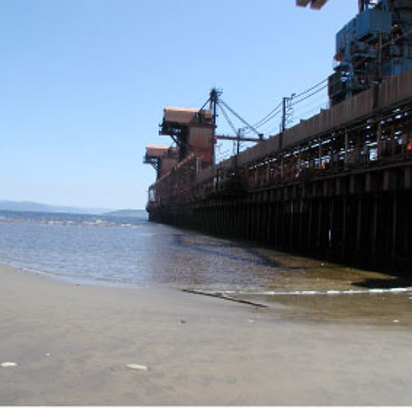
Harsh environment impressed-current CP for large marine loading facility
An Impressed Current Cathodic Protection (ICCP) system utilizing local and remote anodes was installed for a ship-loading facility in Quebec, Canada, to protect the submerged H-piles, cylindrical piles and sheet piles associated with the facility. This facility is subject to extreme ice loading conditions, tides, changing water resistivity, ship traffic and dredging operations.
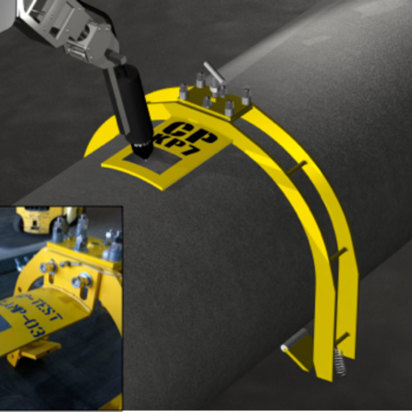
A modern approach to offshore pipeline CP system evaluation
With a significant percentage of the offshore pipeline infrastructure exceeding its original design life, the need for life extension is on the increase. These pipelines will need improved surveillance to evaluate the optimum time to repair (retrofit) and to ensure integrity through the extended life cycle.
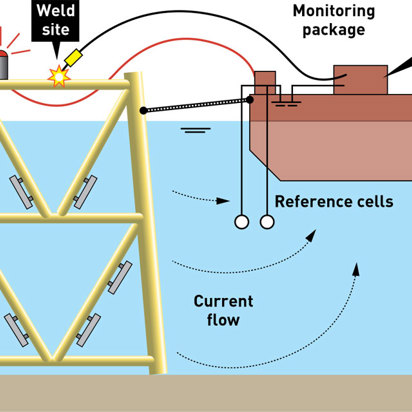
Stray current during marine welding operations
Instances of “inexplicable” pitting corrosion damage have been observed during routine subsea inspections on offshore platforms – even when the platform cathodic protection system has been working as designed. Evidence suggests that this “corrosion” may have been caused by current discharge from the platform during welding operations. This article describes a solution that has been applied successfully on several projects.
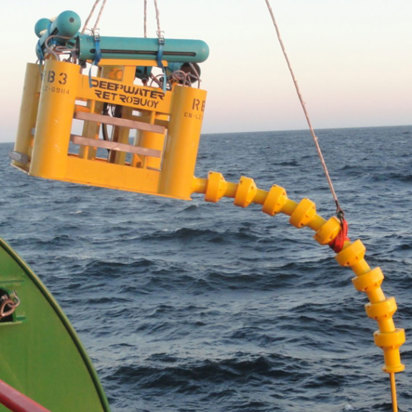
Case studies: New concepts in CP systems for brownfield assets
As offshore infrastructure ages and the price of oil remains low, the corrosion industry is challenged to find better ways to maintain the integrity of subsea structures. In this context, better means more cost-effective; to develop the most cost-effective system we must approach the problem from the owner’s perspective and ask the right questions.
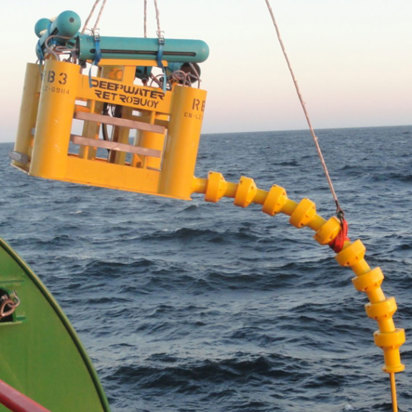
Case studies: Installation of ROV-friendly anode sleds on two deep-water subsea developments
During routine surveillance on two deep-water subsea production fields, Arnold and Oyster, it was noted that some anodes on the well trees and flowlines had excessive depletion. Since the field was undergoing expansion, it was decided to supplement the cathodic protection (CP) systems on all the assets to provide an additional 20 years of life.
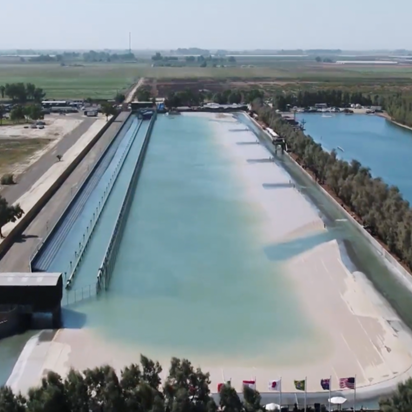
California wave park survey
In January 2020, Deepwater performed a corrosion survey on the nation's most advanced wave pool.