Offshore wind farm
RetroBuoys™ installed on German OWF to replace failing anodes

Introduction
The offshore wind farm in question comprises 80 tripod structures in water depths of 30-40m supporting the turbine. These were protected by an ICCP system using a number of close mounted anodes. On 33 tripod structures the existing anodes were beginning to deteriorate and the levels of cathodic protection current was falling and failing to adequately protect the structures’ submerged steel surfaces. Deepwater carried out an initial estimate of the cathodic protection (CP) current that would be required to provide adequate levels of CP to the tripod for an extended period and this was found to be approximately 280 A, as a mean current requirement. A system providing approximately 400 A would be required to aid final current (i.e. loss of calcareous deposits after a storm event) and extra contingency). We recommended a modified version of the RetroBuoy ICCP anode sled.
Download Case Study (A4)
Download Case Study (US Letter)
Video: RetroBuoy™ installation
Background
Many offshore wind farms utilise sacrificial anode cathodic protection (SACP) systems to protect the external subsea structures supporting the turbine tower. In many areas of the world SACP systems are not allowed to be used for environmental reasons and impressed current cathodic protection systems (ICCP) are specified instead. When this is the case, cathodic protection companies have historically supplied close mounted anode systems based on marine designs which are not ideal for this application. Marine, or ship systems, rely on the fact that the hull of the vessel is coated and that every 5 years the vessel is dry docked and the coating repaired. This is not possible with an offshore wind farm structure which in any case usually has a large area of uncoated steel.
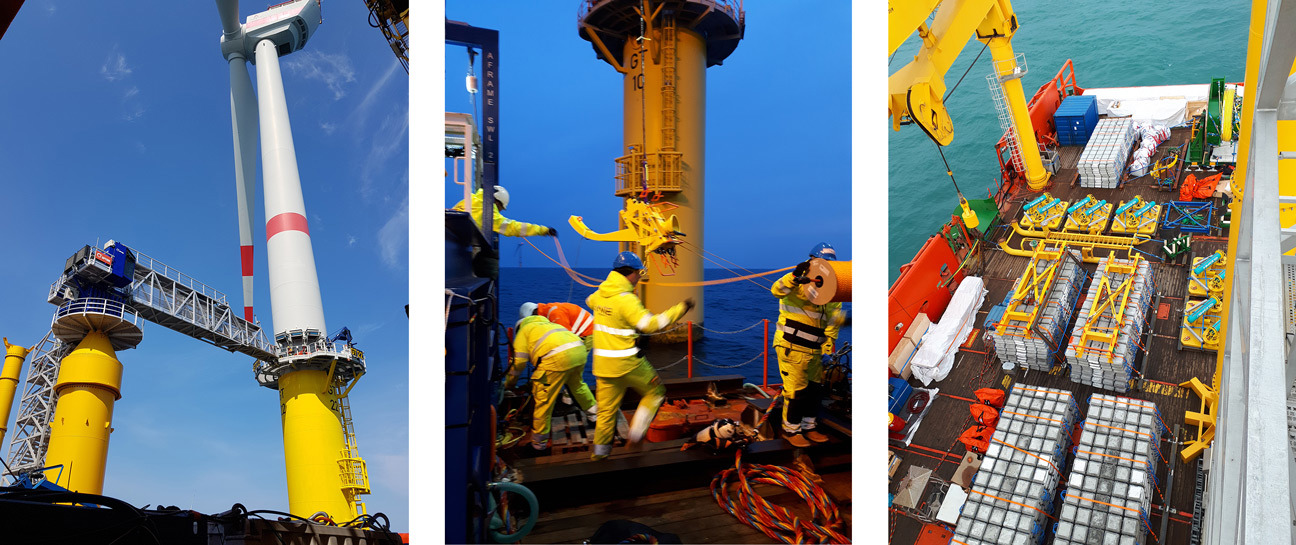
ICCP system design
A CP modeling study was initially carried out in order to prove that CP could be provided by one or more remote ICCP anode sleds. The model also confirmed the optimum remote location for the anode sled. In this instance an ICCP system with remote anodes, was considered the safest economical solution, i.e. lowest involvement of divers. Close mounted impressed anodes would require significant installation time, in addition to the risks associated with cable routing and cable protection. Therefore, an ICCP system utilising remote anode sleds was considered the only practicable solution to meet the current demand.
ICCP systems require a DC power source to impart a larger voltage at the anode, thereby making the system able to generate far more current for a given anode size. A DC power supply, typically either a transformer rectifier / power supply unit, is required to increase the voltage and therefore the current output capacity. The current is conducted to the anode from the power source via a subsea anode cable, then from the anode through the electrolyte (in this case seawater) surrounding the structure. The current enters the structure and is conducted through the steelwork to the negative output of the DC power supply, which completes the circuit. At the surface of the structure where the current enters the structure from the seawater, the electrochemical potential at anodic sites is shifted from the anodic state (corroding) to the cathodic state, preventing galvanic cells from forming and preventing corrosion.
There are no standards particularly written around CP retrofit, either galvanic or impressed current, so retrofit calculations are in the main calculated around existing standards that specify a variety of current densities for new structures and applying known historical operational or retrofit data. When the structure starts to depolarise, extra care is required to achieve the initial boost to the system to re-establish a polarised level.
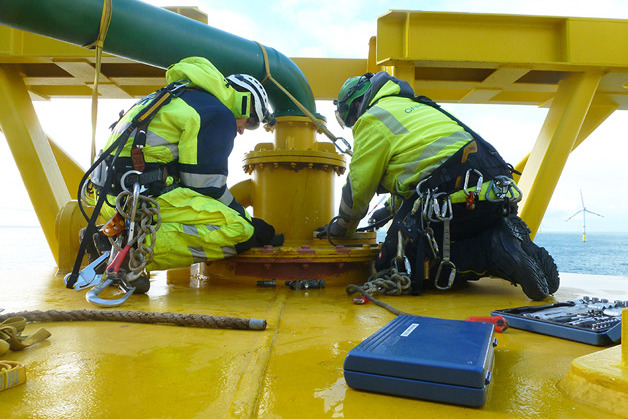
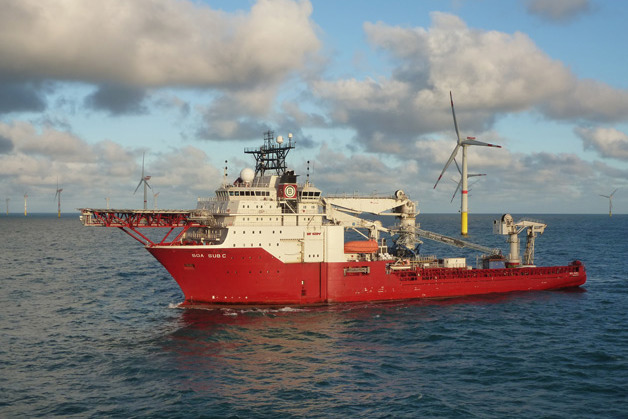
The system
The proposed system was based on the successfully tried and tested remote ICCP RetroBuoy system and consisted of the following key components:
- RetroBuoy Junior (seabed mounted impressed current anode sled)
- Subsea anode power cable (DC) (including, subsea armour termination and bend restrictor)
- Cable hang-off assembly
- Subsea Cable Protection Assembly (SCPA)
- Subsea Cable Protection Clamp (SCPC)
- Topside anode junction box
- Power Supply Unit (PSU), switch mode type
- Positive and negative topside power feed cables (DC)
- Structural negative connection
- Concrete mattresses for subsea anode power cable seabed stability
Additionally, a monitoring system was fitted to each ICCP system, to control, monitor and log the following:
- 3 No. existing fixed external zinc reference electrodes
- 2 No. existing fixed internal zinc reference electrodes
- PSU Voltage and Current
- Various status alarms
The monitoring system was incorporated into the PSUs to monitor and log via an Ethernet connection into the existing communication network to the client’s onshore facilities. Each tripod ICCP system is rated at 48 Volts 500 Amps DC. The positive DC power feed to the RetroBuoy Junior was provided by a subsea anode power cable, with the negative return path through the seawater.
The subsea anode power cable was terminated to the RetroBuoy Junior prior to over-boarding using a specially developed dry-mateable connector. The subsea anode power cable was routed from the RetroBuoy Junior, located on the seabed, to the anode junction box on the turbine above the gas tight floor via an I-tube held in place by a subsea cable protection clamp (SCPC). The anode cable was routed along the seabed from the touchdown point to the RetroBuoy Junior and located on the seabed approximately 28 m from the centre of the tripod. The relative locations were the same for all tripods. Due to the amount of scour and the depth of the entry point into the tripod for the cable, where the I-tube will be located, the cable is protected by a subsea cable protection system from the seabed to inside the tripod. One of the key design criteria was that the system had to be installed in a short period of time with all items of the system deployed from the installation vessel with no special heavy lift equipment.
The Power Supply Unit was modular so that it could be easily handled onto the turbine and taken to the location and assembled, the concrete stabilisation mattresses were assembled quayside with local labour and concrete. The subsea cable for the RetroBuoy Juniors was spooled onto a single deployment reel in finished lengths and the cable protection system was supplied in kit form for assembly on the deck of the vessel.
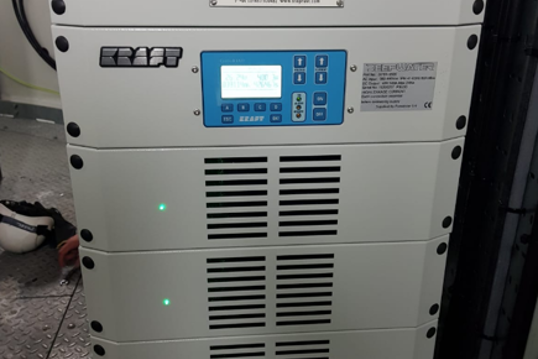
Modular power supply unit
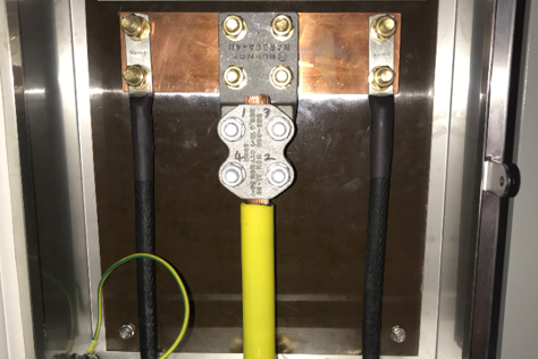
Junction box
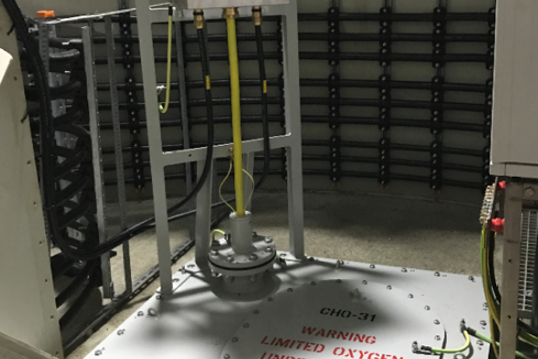
Junction box with new hatch
Installation
Up to four complete retrofit ICCP retrofit systems were taken to the field on the installation vessel at a time. Specially designed installation and deployment equipment was used to speed up the installation process including a mattress deployment frame, all subsea equipment was designed to be installed by ROV without the need for diver involvement. Topside equipment was transferred from the vessel onto the turbine and a new cable access hatch installed. The power supply unit, junction boxes and topside cabling was installed by teams on the tower whilst teams on the vessel simultaneously prepared the subsea equipment. The subsea cable protection clamp was located on the turbine and secured by the ROV.
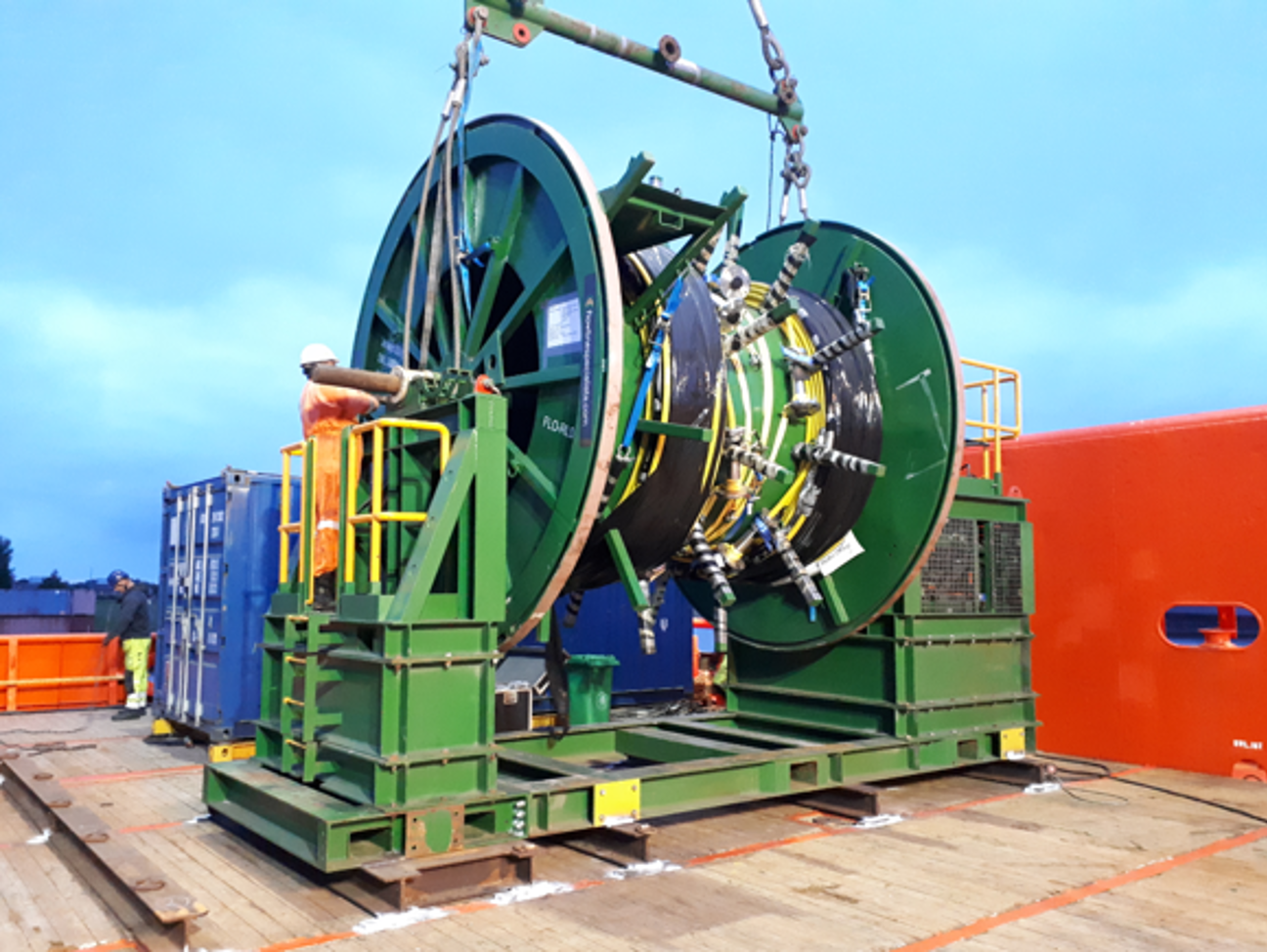
On the vessel, the cable was connected to the RetroBuoy anode system using a dry-mateable connector and the cable protection system installed. The RetroBuoy was then lowered to its final position on the seabed.
The subsea cable and cable protection system was pulled through the clamp, secured and terminated topside.
Cable stabilisation mattresses were deployed around the RetroBuoy and along the full cable route. The buoyant anode floats on the RetroBuoy were deployed, the power supply was energised, and the system commissioned. Cathodic protection was restored to the turbine structure - The whole process taking less than 24 hours from deployment to commissioning.
Summary
The complete system was specifically designed for the application and had to be installed without diver intervention, in addition there was a very narrow installation window due to weather conditions. Deepwater met these challenges and with cooperation from the operator and other subcontractors achieved the target of reinstating specified levels of cathodic protection to the turbine subsea structures.
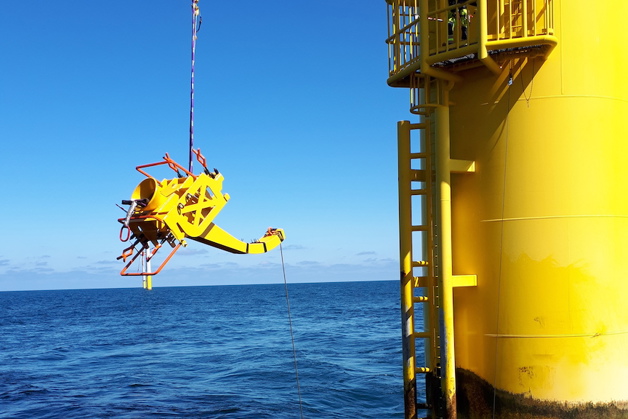
Subsea cable protection clamp
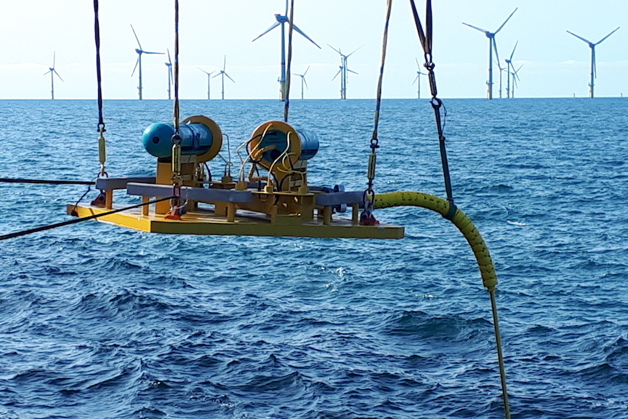