WHITE PAPER
The cost of a bad pipe support
In the 30 years since we’ve developed I-Rod® pipe supports, Deepwater Corrosion Services has been contacted by many companies to analyze all kinds of pipe support failures on all sorts of design. Almost every one of these failures can be traced back to a poor decision in the initial design, purchasing, or installation of the supports. No two failures are exactly the same, but they all have one thing in common: they cost the operator money in repairing a failed support.
What is the cost of a bad decision that has caused a failed support? After encountering so many prematurely failed supports, we worked with operators around the United States to examine the near-term price many pay for short-term savings.
There are many variables that can impact repair costs. Location is one of the most significant. Wages differ dramatically between workers onshore in New Mexico and offshore in the Gulf of Mexico. Let’s assume a failed support is onshore and that a bad decision was made during the front end of a new construction project by the engineering group that designed the system.
The system will be located in the open area of an oil terminal and tank farm. The engineering group selected FRP pads/shoes to be installed between the pipe and the metal support. What they did not know was that the FRP pad design can cause significant corrosion and damage in as little as one year. Here is an image of this type of damage from a site where the FRP had been in service for less than two years:
Figure 1 - Cost to repair failed FRP
Figure 2 - The FRP above had been in service for less than two years.
To repair the damage from this installation will require non-destructive testing to determine the amount of metal wall loss that has occurred. If the pipe is deemed safe for continued operation, the contractor will need to lift the pipe. That will require a forklift, crane, or other similar equipment. After the pipe is raised, it will need to be media blasted to remove the damaged coating, remaining glue, and corrosion. After the pipe is cleaned and prepped, it will need to be re-coated and painted. All of this repair work utilizes some valuable resources; a forklift or crane, a two-person inspection crew, and a three or four-person construction crew.
According to a client in the Midwestern USA, the cost for this work at this one, easy to access location would be a minimum of $1,000 for pipe sizes 12” and under. The price per location increases incrementally with the pipe size increase to well over $2,500 per support location on a 24” pipe.
A West Coast USA operator tells us the cost for the same work at the same easy to access location will be closer to approximately $2,800 for pipe sizes 12” and under. The price per location would then increase incrementally with the pipe size increase to well over $4,000 per location on a 24” pipe. The factors that comprise the repair totals vary, but three primary factors are consistently the most significant indicators of cost:
1. Site location: Some locations are easy to access and the level of risk is relatively low. Other locations require qualified personnel, unique transportation to access, or have limited hours per day to perform the work. Each of these locations have costs associated with getting people, tools, and equipment to the repair site. Some of these costs can get very high.
2. Pipe location: The location of a pipe may require special equipment to access. Some locations can be accessed by standing on the ground while others may require a rope access team, a scissor lift, a boat, or other expensive vehicle.
3. Required work permits: Will there be hot permits, access permits, or specialty access permits? Each of these permits has additional associated costs.
Some other factors that will influence the cost of inspecting and repairing a damaged pipe include weather, international visas, injuries, insurance, wages for the area, union influence, and repairs that require replacing the pipe. The three primary factors and these additional ones can increase the cost to repair a pipe damaged at the pipe support location to $10,000 per location or more. These costs do not take into account the lost income due to shutting down a plant, terminal, or pipeline in order to perform the repair. If the pipe wall loss caused by the corrosion is significant enough to render the pipe unsafe for continued use and the pipe must be removed and replaced, the cost can reach well over $100,000. If a pipeline transporting flammable materials experiences catastrophic failure due to unnoticed corrosion, the costs can go well into the millions. The best decision is to avoid these costs by specifying and purchasing genuine I-Rod®. Don’t make a poor decision to specify a bad design or purchase an inferior product and spend $1,000 to $10,000 per support location repairing hazardous damage every couple years. Trust your pipes to the field-proven solution that lasts for decades. For more information on the best way to prevent crevice corrosion on your pipe support design visit i-rod.com.
The cost of a bad pipe support
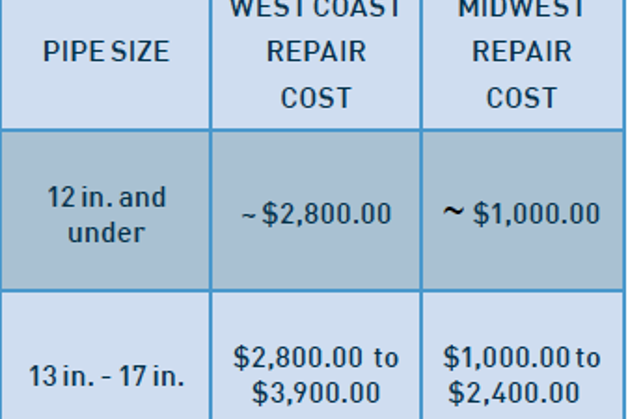
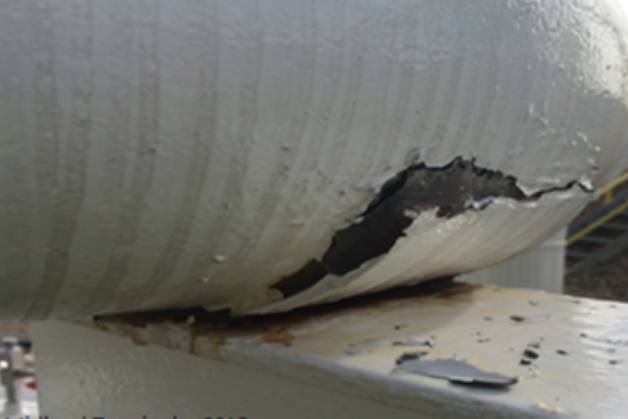
The results of failed FRP
The FRP above had been in service for less than two years.