Hydrogen embrittlement study
Hydrogen embrittlement study for major well services and equipment provider
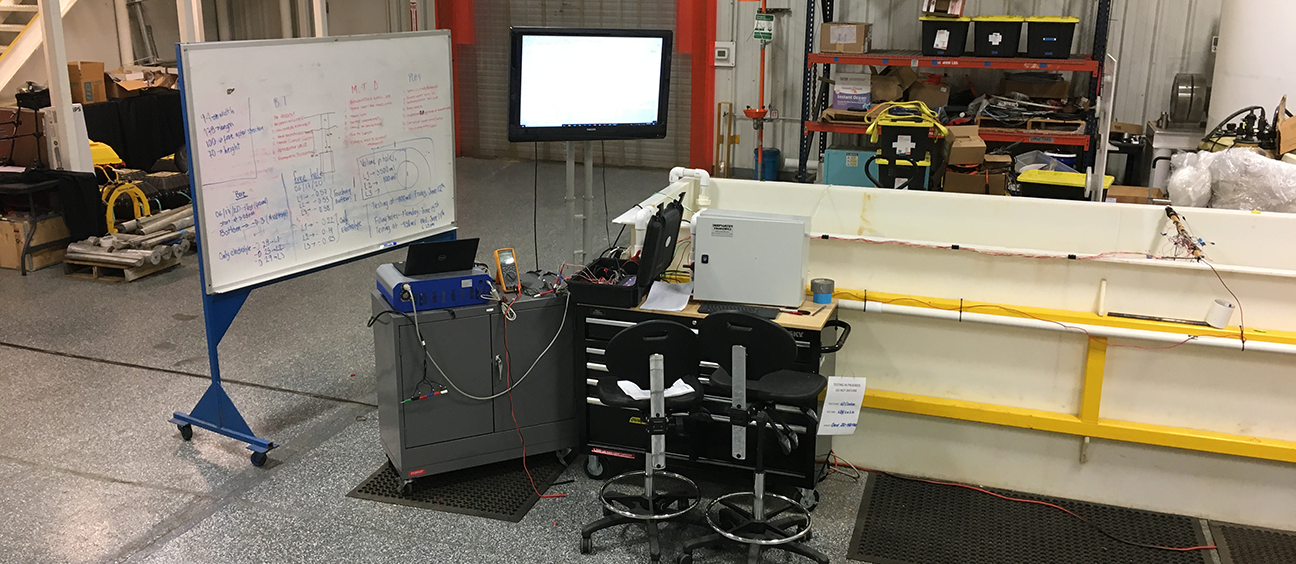
Project overview:
Deepwater Corrosion Services Inc. (DCSI) was contracted to conduct laboratory testing including potential monitoring of a clamp connector subject to cathodic protection (CP). It was unknown if the CP current reached the 725-alloy (UNS N07725) gasket inside the clamp connector. Furthermore, the effects caused by the CP on the gasket material were also unknown; as indicated by personnel involved, one of the main concerns is that the polarization of the Inconel gasket could generate hydrogen, leading to potential hydrogen embrittlement when the CP level is excessive.
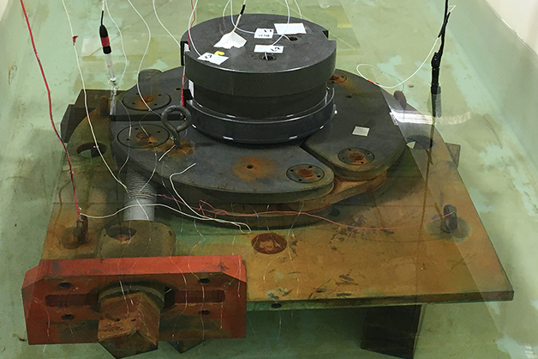

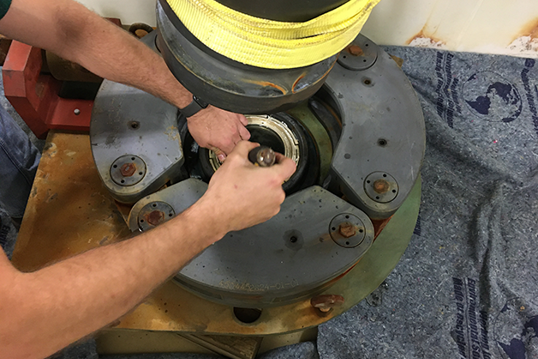
Background:
Subsea connections include flowline connections and umbilical control connections. The types of subsea flowline connection can be broadly divided into four types of connections: welded, flanged, clamp hub, and mechanical connections. The welded connection is normally used for subsea connections in very shallow water, and the welding procedure is carried out in a one-atmospheric chamber to achieve a dry environment. For the other three types of subsea connections, the primary purpose of the connection method is to create a pressure-tight seal that resists the loads associated with subsea environments. The mechanical connectors use either a mandrel or hub style interface and the actuating tools are hydraulically or mechanically actuated. Clamp hub connectors may use the same metal ring gaskets as bolted flange connectors or use proprietary gasket designs. The clamping device forces the mating hubs together as the clamping device is tightened. Rotational alignment is unnecessary since the mating hubs do not have bolt holes, except for multi-bore hubs. On the other hand, most clamped hubs do not permit the amount of initial misalignment that bolted flange connections may provide. The characteristics of clamp hubs are summarized as follows:
The clamping device preloads two hubs as the device is tightened.
•A metal gasket is compressed between the two hubs to create a seal.
•It can be made up by divers or ROV-operated tools
•It is faster to make up than a bolted flange because it has fewer bolts.
•Hubs must be closely aligned before makeup. Rotational alignment is not critical.
The connector designs can vary to accommodate a wide range of configuration needs and to provide a high degree of installation versatility and operational reliability. Since 1998, more than 2,500 OSS connectors have been installed in more than 80 projects worldwide for connecting flowlines and export lines. Included in the design, the metal sealing technology is one of the components that allows corrosion resistance and flexibility for the different configurations; Dual Metal Gasket (DMG) is a technology that allows for both flexibility and corrosion resistance.
The DMG is made of Inconel 725-alloy (UNS N07725) with high resistance to temperature, pressure, and corrosion; despite these characteristics, Inconel 725-alloy couplers cracked in service conditions in 2015. The failure was attributed to hydrogen embrittlement, and the conditions were re-created by simulating service conditions with a CP level of -1200 mV vs Ag/AgCl (seawater). Since no electrochemical tests were carried out, it was imperative to carry out potential and current monitoring of the clamp in service conditions to determine the effect of the CP in the gasket.
Scope:
The scope of the work was to determine the presence and extent of cathodic protection polarization inside the OCS clamp connector, specifically the alloy 725 gasket inside the subsea connection assembly. In order to achieve the target, Deepwater Corrosion Services carried out laboratory testing to measure the electrochemical potential in a total of nine locations inside and outside the clamp. Some of the locations required machining of the connector for introduction of Luggin capillaries, allowing the introduction of micro reference electrodes for potential measurements at well defined, highly localized test points. Three levels of external CP polarization were achieved by using an impressed-current cathodic protection (ICCP) system using an in-house Transformer Rectifier (T/R), anode and grounding system. Additional SACP testing was carried out using an aluminum sacrificial anode.
Results:
It was assumed that the CP had caused the hydrogen embrittlement occurring on the Inconel gaskets; however, there was no proof that the CP reached the failed gasket. It is also important to note that the results from this work were obtained under laboratory conditions and not in the field under service conditions.