Platform anode retrofit

There is no design code for anode retrofit
Unlike designing anode systems for new platforms, a retrofit designer must consider the state of the remaining cathodic protection. Often, this data is not available and the designer must make assumptions based on past experience. This is where Deepwater's engineers have a big advantage, as they've retrofit new anodes on more fixed platforms worldwide than anyone else.
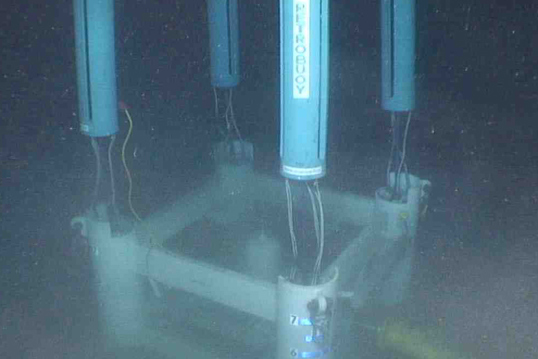
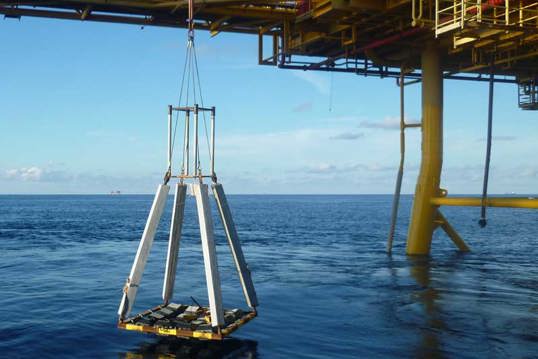
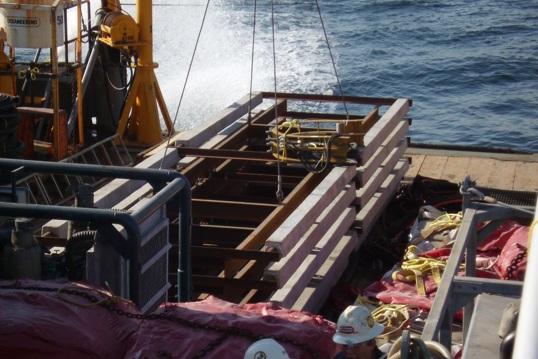
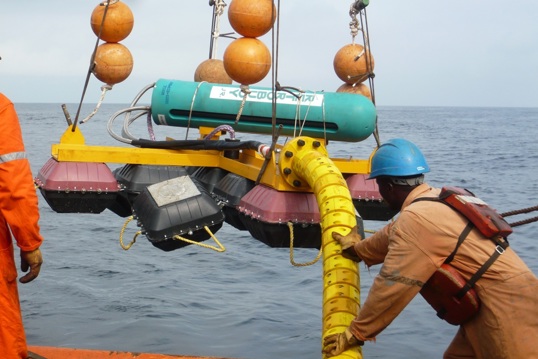
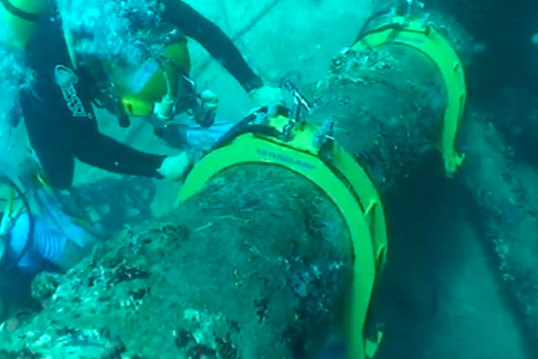
One-for-one anode replacement
Diver welding on a new anode
Underwater welding
Early methods of replacing consumed anodes involved a one-for-one replacement using underwater welding. This method is extremely expensive, so it wasn't long before operators sought more economical methods.
Dual anode clamp-ons
Rather than welding, divers can bolt anodes to structural members and electrically connect the anode to the structure using a contact screw.
Diver bolting on a dual anode
More efficient designs
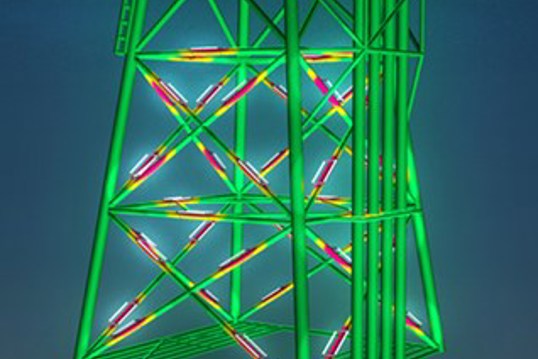
Close-mounted anodes
Anodes that are welded or bolted to a structure only "throw" CP current so far. This means that dual clamp-on anodes are not performing individually to their full capacity.
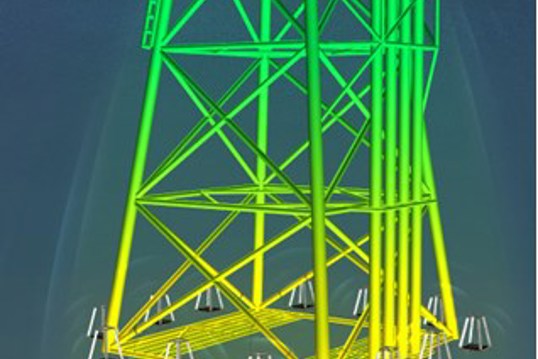
Semi-remote anodes
If anodes are positioned just a little bit farther from the cathode (the structure), the current "thrown" from the anode can protect more steel. This means that a structure can be retrofit with fewer anodes and still be equally protected.
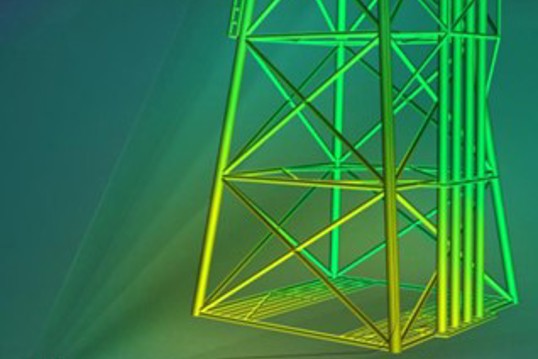
Impressed current
If a structure has power and the surface area of the jacket is large enough, an impressed-current anode sled can provide enough current to protect 80,000 sq ft of steel.